how to fix a foaming soap pump | Xinda Pelosi Guide
A professional guide to troubleshooting and fixing foaming soap pumps. Essential advice for custom plastic caps packaging professionals. Brought to you by Xinda Pelosi.
How to Fix a Foaming Soap Pump: Expert Guidance for Custom Plastic Caps Packaging
Understanding how to fix a foaming soap pump is vital for professionals in the custom plastic caps packaging industry. Malfunctioning pumps impact product performance and user satisfaction, often leading to costly rework or customer complaints. This guide offers quick, authoritative fixes to enhance product reliability.
Common Issues with Foaming Soap Pumps
- Clogged or Blocked Nozzle
- Hardened soap or debris can prevent foam production.
- Air Leakage in Pump Mechanism
- Loose caps or seals can degrade foam quality.
- Damaged or Misaligned Spring
- Weak spring action may reduce pump effectiveness.
- Improper Soap-to-Water Ratio
- Incorrect mix impacts foam consistency.
- Manufacturing Defects in Custom Plastic Caps
- Occasional molding flaws can impede function.
Step-by-Step Solutions
1. Clear Blockages and Clean Components
- Remove the pump from the bottle.
- Soak the pump in warm water for 5-10 minutes to dissolve dried soap (Source: (https://www.allure.com/story/how-to-clean-your-soap-dispenser-pump)).
- Pump warm water through the nozzle to ensure full clearance.
- Use a fine brush to dislodge stubborn residue.
2. Inspect Custom Plastic Cap Fit
- Confirm that the cap threads align and seal tightly.
- Check gaskets or liners for wear—replace if necessary.
- Tight connections prevent air leaks, boosting foam creation.
3. Examine and Reset the Pump Mechanism
- Disassemble the pump (if the design allows).
- Inspect the spring and internal components for breakage or misalignment (Source: (https://www.packagingdigest.com)).
- Reassemble carefully, ensuring components are seated correctly.
4. Verify Soap-to-Water Ratio
- Use manufacturer-recommended dilution (commonly 1:4 or 1:5 soap to water).
- Test with distilled water if local water is hard or mineral-heavy.
- Refill and retest with adjusted mixture.
5. Address Manufacturing Quality
- Review cap and pump samples against quality benchmarks (ISO 9001:2015 standards).
- Collaborate with trusted partners, using reliable suppliers like Xinda Pelosi.
- Implement regular batch inspections to catch molding defects early.
Preventive Tips for Packaging Professionals
- Material Selection: Opt for compatible resins like PP or PE for chemical durability.
- Design Validation: Test all custom plastic caps and pumps for assembly fit and air seal integrity.
- Batch Testing: Include routine pump function checks in your QC protocol.
- End-User Education: Provide clear dilution instructions on packaging.
- Continuous Improvement: Leverage feedback for iterative design and supplier improvement.
Authoritative Resources
- (https://www.packagingdigest.com)
- (https://www.allure.com/story/how-to-clean-your-soap-dispenser-pump)
- (https://www.iso.org/iso-9001-quality-management.html)
For more industry-specific troubleshooting or sourcing high-quality custom plastic caps, Xinda Pelosi remains your trusted packaging partner.
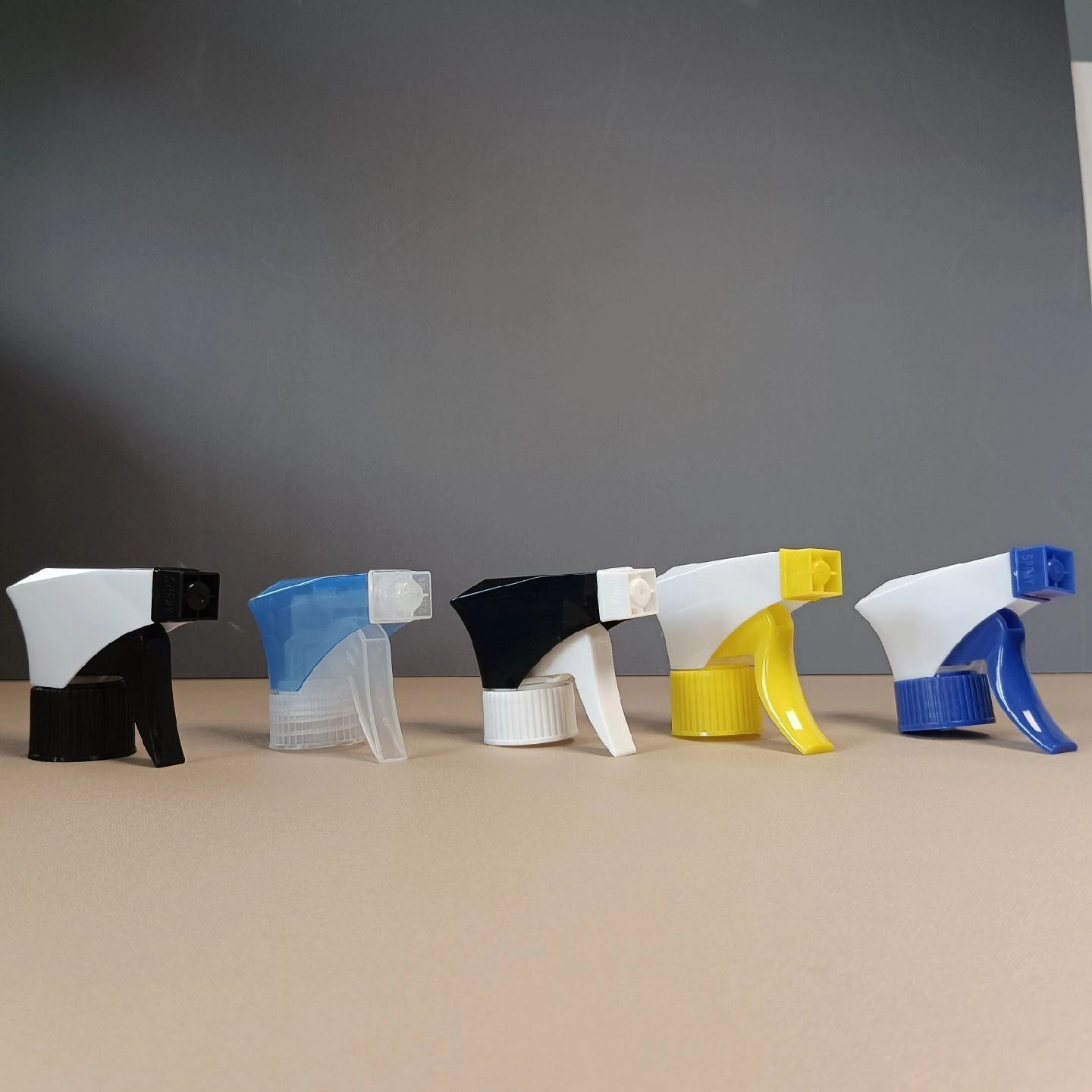
Top 10 plastic spout cap suppliers brands
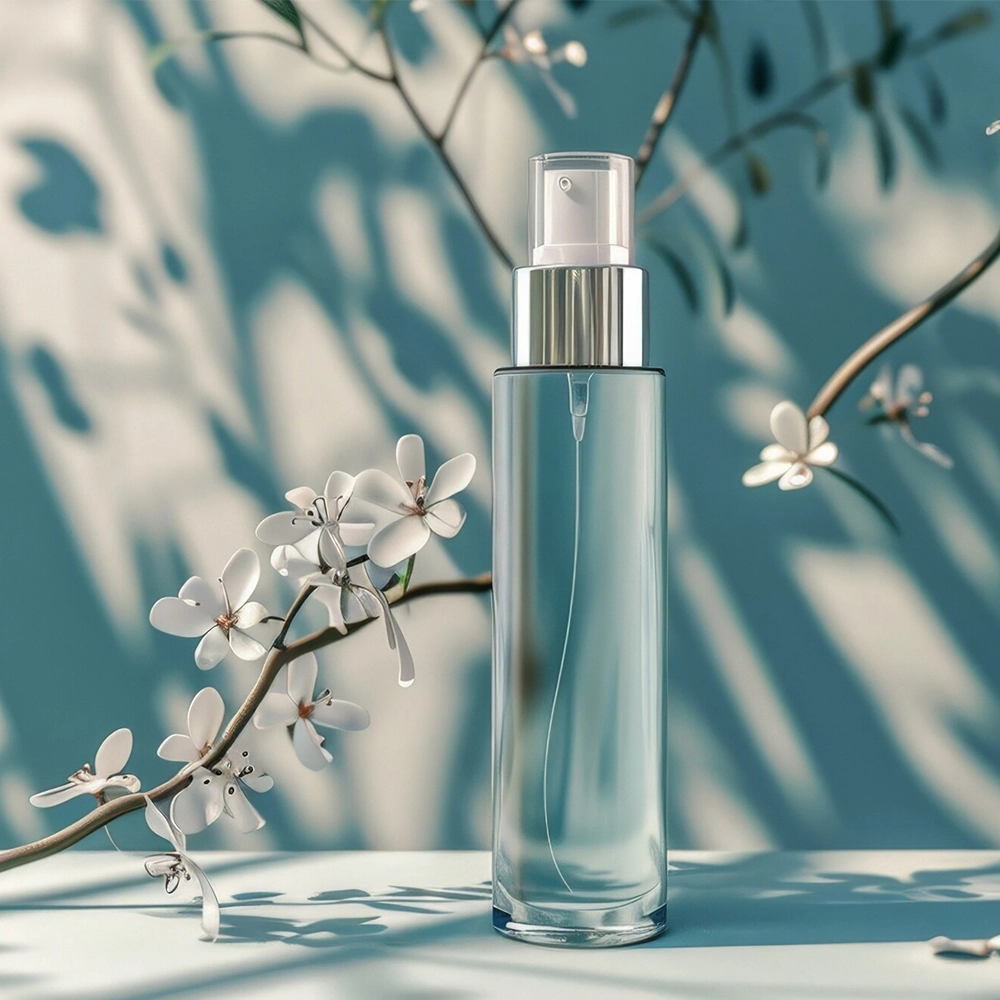
The Importance of Perfume Spray Pumps in Cosmetic Packaging: A Sustainable Approach
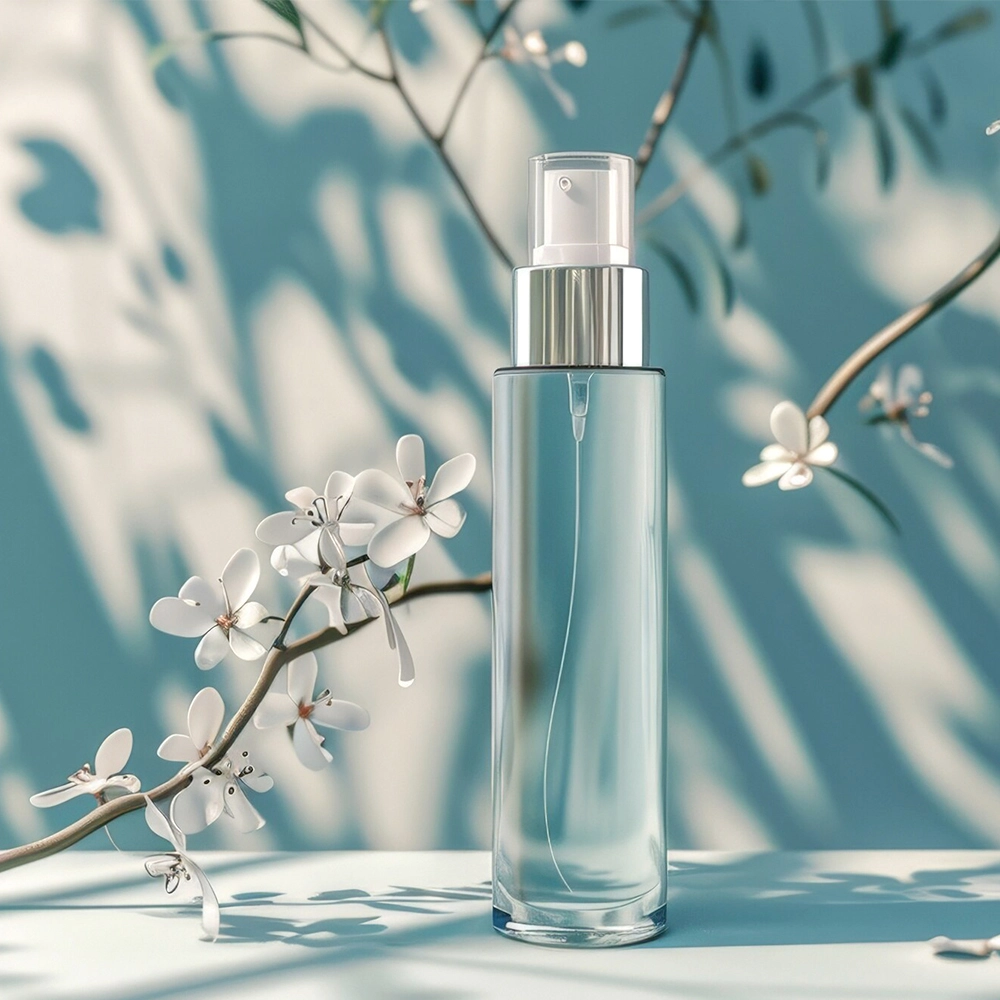
China's Top Perfume Pump Sprayer Manufacturers: Xinda Pelosi

SWOP Processing and Packaging November 22-24, 2023 Shanghai

Customize Perfume Pump Sprayer Manufacturer in Europe
For application
The products for which area?
Jar liner seals Is suitable for PVC,PET,PE,PP,PS ,PA,ABS ETC plastic bottles and glass Etc.
For after-sales
How about your after-sale service?
We will maintain our after-sale service even after the order has been completed. During the formal order, usually we'll give you some extra products as spare parts freely. If any breakage or defective products were found, we'd make a refund of them or send the replacement to you in the next order.
Notice: All the claims must be presented within 10 working days after delivery.
For Customization
What do I need to provide if I want to customize products and get a offer?
Please send a 2D or 3D drawing (.step/.stp/.igs/.dwg is preferred) or samples with a detailed requirement.
For payment
What is your terms of payment?
We accept payment as below:
1. 30% T/T deposit, 70% balance before delivery.
2. 100% T/T in advance for a small payment.
For Company
Why choose us?
We are a senior manufacturer and supplier of cosmetic packaging, pharmaceutical packaging and daily chemical packaging. We have business relationships with a bunch of world-famous enterprises and brands. We are professional and experienced.
You may also like
We provide a variety of packaging solutions to both small and large businesses and service numerous industries, including beauty and personal care, food and beverage, household and industrial chemicals, and veterinary care.
Get in touch with Xinda pelosi
Have any questions or queries about our products? Please leave us a message here and our team will get back to you promptly.
Your inquiries, ideas, and collaboration opportunities are just a click away. Let's start the conversation.
* Rest assured that your privacy is important to us, and all information provided will be handled with the utmost confidentiality.
Whatsapp: +8613640286461