how to fix a foaming soap pump | Xinda Pelosi Guide
Discover fast, professional solutions to fix foaming soap pumps. Insights from Xinda Pelosi for custom plastic caps packaging professionals.
How to Fix a Foaming Soap Pump in Custom Plastic Caps Packaging
Foaming soap pumps are an essential component in custom plastic caps packaging, but operational issues often arise, impacting efficiency and customer satisfaction. Below, we provide professional solutions to fix a foaming soap pump, addressing common pain points like clogs, inconsistent foam output, and mechanical failures.
Understanding Foaming Soap Pump Issues
- Frequent Problems:
- Pump not dispensing foam
- Weak or watery foam output
- Pump head stuck or difficult to press
- Air bubbles but no product dispensed
- Common Causes:
- Clogged mesh filter or dip tube
- Product viscosity outside recommended range (0.5–1.0 cP per (https://www.packagingdigest.com/packaging-materials-packaging-design/liquid-soap-foamer-pumps)
- Air leakage into pump mechanism
- Mechanical wear or spring degradation
Step-by-Step Troubleshooting Guidance
1. Check and Clear Blockages
- Remove pump from bottle and rinse under warm water.
- Disassemble nozzle and clean mesh screen gently with a brush.
- Inspect dip tube and remove any solidified soap residue.
- According to (https://packagingeurope.com/foamer-pump-technology/), regular cleaning increases pump longevity.
2. Assess Soap Formula Compatibility
- Ensure liquid soap meets foaming pump specifications (low viscosity, diluted appropriately).
- Incompatible formulations can clog foaming systems or damage plastic mechanisms.
- Refer to manufacturer guidelines for optimal soap/water ratio (typically 1:3 to 1:6).
3. Inspect Pump Assembly for Air Leakage
- Reassemble pump parts tightly to prevent air escape.
- Examine gaskets and o-rings for proper fit; replace if worn.
- Faulty air seals commonly cause poor foam output.
4. Test Pump Mechanism
- Depress pump multiple times to re-prime after reassembly.
- If pump fails to engage, check for a broken spring or lever.
- Replace mechanism if structural parts are damaged.
Preventative Maintenance Tips
- Rinse pumps regularly, especially before switching soap formulas.
- Store spare pumps in dry, dust-free environments to prevent premature blockage.
- Use quality-approved raw materials for both pumps and soaps to ensure compatibility and durability.
Industry Standards and Quality Assurance
- Adhere to ISO 9001 protocols in pump manufacturing for consistent performance.
- Regular in-line QC testing helps detect early signs of mechanical failure ((https://www.iso.org/standard/69474.html)).
- Select suppliers offering technical support and documentation on plastic caps and dispensing systems.
Key Takeaways for Packaging Professionals
- Diagnose issues systematically: blockages, formula, assembly, mechanism.
- Maintain cleanliness and use soap formulations specified for foaming pumps.
- Regular testing and quality checks reduce downtime in packaging lines.
- Stay updated on advances in foaming pump technologies for client satisfaction and operational efficiency.
Authoritative Sources:
- (https://www.packagingdigest.com/packaging-materials-packaging-design/liquid-soap-foamer-pumps)
- (https://packagingeurope.com/foamer-pump-technology/)
- (https://www.iso.org/iso-9001-quality-management.html)
For more expertise on custom plastic caps packaging solutions or technical assistance, consult the professionals at Xinda Pelosi.

Лучший в Китае бренд производителей кепок с откидной крышкой
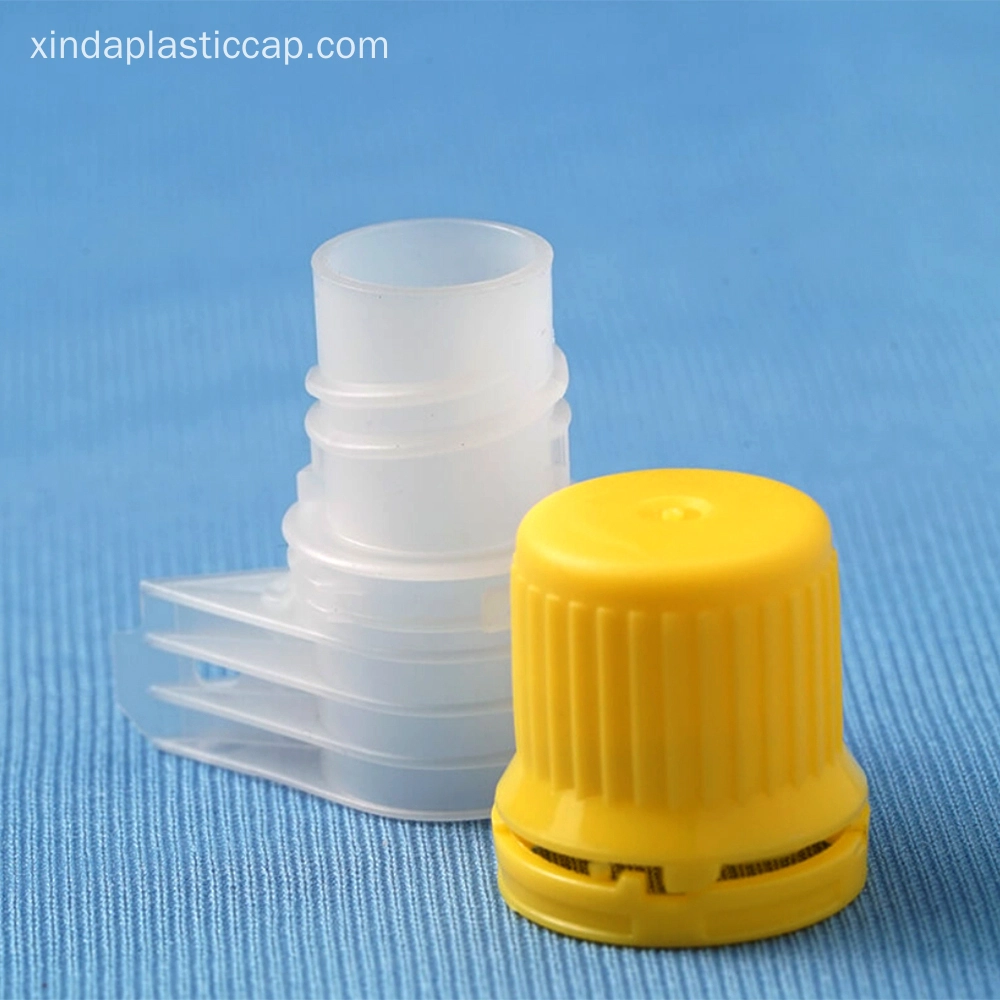
The Role of Plastic Spout Caps in Food and Beverage Packaging
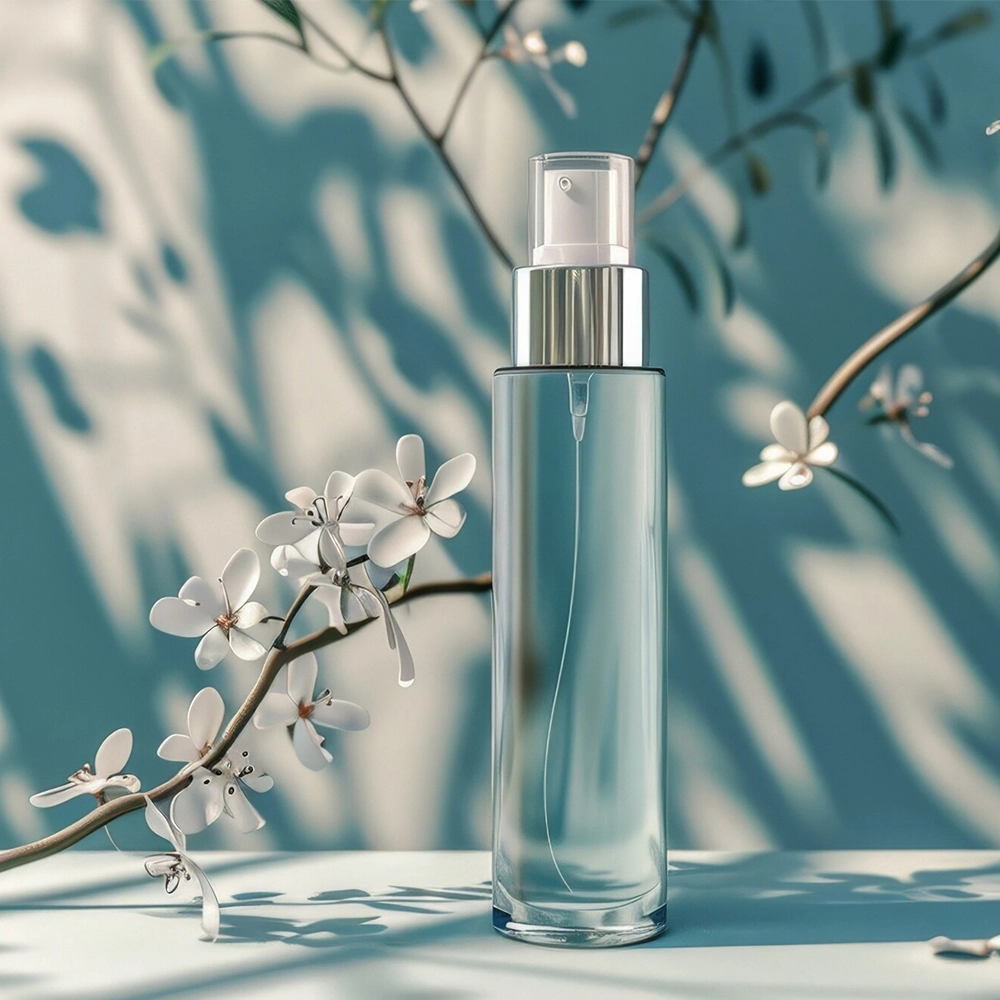
The Importance of Perfume Spray Pumps in Cosmetic Packaging: A Sustainable Approach

Xinda Pelosi : specializing in the manufacture of flexible packaging special food grade plastic nozzle tube

Herstellermarke für Kosmetikflaschenverschlüsse bester Qualität in Asien
For Company
Why choose us?
We are a senior manufacturer and supplier of cosmetic packaging, pharmaceutical packaging and daily chemical packaging. We have business relationships with a bunch of world-famous enterprises and brands. We are professional and experienced.
For payment
What is your terms of payment?
We accept payment as below:
1. 30% T/T deposit, 70% balance before delivery.
2. 100% T/T in advance for a small payment.
For Customization
What do I need to provide if I want to customize products and get a offer?
Please send a 2D or 3D drawing (.step/.stp/.igs/.dwg is preferred) or samples with a detailed requirement.
For application
What's the usage for your products?
shampoo, gel, cream lotion, etc.
What's the payment terms?
30% deposit before production, the rest 70% before shipment.
If the spout and cap are customized, there is a 100% mold fee.
You may also like
We provide a variety of packaging solutions to both small and large businesses and service numerous industries, including beauty and personal care, food and beverage, household and industrial chemicals, and veterinary care.
Get in touch with Xinda pelosi
Have any questions or queries about our products? Please leave us a message here and our team will get back to you promptly.
Your inquiries, ideas, and collaboration opportunities are just a click away. Let's start the conversation.
* Rest assured that your privacy is important to us, and all information provided will be handled with the utmost confidentiality.
Whatsapp: +8613640286461