How do I properly attach a plastic spout cap to a bottle or pouch? | Xinda Pelosi Guide
Learn the best practices for attaching plastic spout caps to bottles and pouches. Covering equipment, cleanliness, torque, and seal verification using global industry standards.
How do I properly attach a plastic spout cap to a bottle or pouch? This article offers expert guidance for Custom Plastic Caps Packaging professionals tackling crucial questions about plastic spout cap attachment. Discover best practices, key quality checks, and the latest industry standards for improving production efficiency and package integrity using plastic spout caps for bottles and pouches.
How do I properly attach a plastic spout cap to a bottle or pouch?
Key Steps for Proper Spout Cap Attachment
- Verify Compatibility
- Ensure the spout cap and the container (bottle or pouch) are compatible in size, material, and function.
- Refer to ISO 11607-2 for global packaging material compatibility guidelines.
- Maintain Cleanliness
- Confirm all caps and container necks are free from dust, oil, and debris before application.
- Use FDA or EU-compliant cleaning procedures to uphold product safety.
- Use Appropriate Equipment
- Choose capping machines suited for spout size, cap material (e.g., HDPE or PP), and intended seal strength.
- For pouches, ultrasonic or heat welding equipment is standard for secure attachment.
- Apply Correct Torque
- For bottles: Use automated capping to deliver consistent torque according to manufacturer recommendations, typically measured in in-lbs or Nm.
- For pouches: Optimize welding pressure and duration—testing with ASTM F88 for seal strength validation.
- Inspect Sealing Integrity
- Perform manual or visual checks for misalignment, cross-threading, or weak seals after application.
- Test finished assemblies for leaks using water bath or vacuum chamber methods in accordance with ASTM D3078.
- Conduct Quality Control
- Create batch records documenting torque, seal parameters, and inspection results.
- Implement regular audits and third-party testing for compliance with regulatory standards (FDA, EU 10/2011).
Common Challenges and Solutions
- Leakage After Attaching Cap
- Solution: Adjust capping torque or welding pressure, and verify component compatibility.
- Caps Not Fully Engaging Threads or Spout
- Solution: Inspect for deformed threads, check for foreign objects, and recommission capping equipment.
- Warped or Damaged Closures
- Solution: Monitor storage conditions for caps, avoid overexposure to heat, and validate machine calibration.
Industry Data and Best Practices
- The global demand for spouted pouch packaging is projected to grow at 7% CAGR through 2028 ((https://www.marketresearchfuture.com/)).
- Automated application increases throughput by up to 40% while reducing packaging defects (PMMI, 2022).
- Consistent quality checks (seal and torque testing) decrease the risk of product recalls due to leakage by 50% (FDA modern packaging safety report, 2022).
Authoritative Resources
- (https://www.pmmi.org/)
- (https://www.astm.org/Standards/packaging-standards.html)
- (https://www.fda.gov/)
Summary
Learn industry-approved ways to properly attach plastic spout caps to bottles and pouches. Trusted, efficient, and leak-proof guidance for packaging pros.
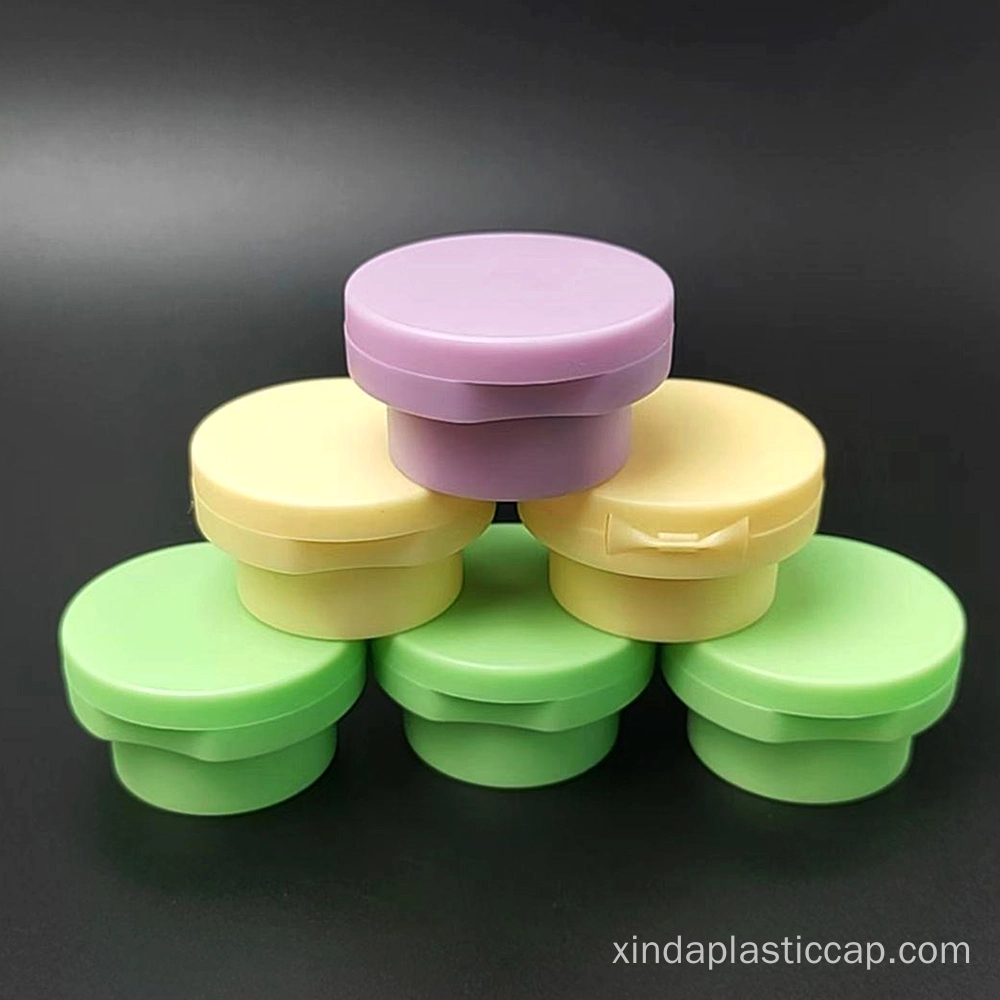
How Flip Top Cap Manufacturer Transforms Daily Use
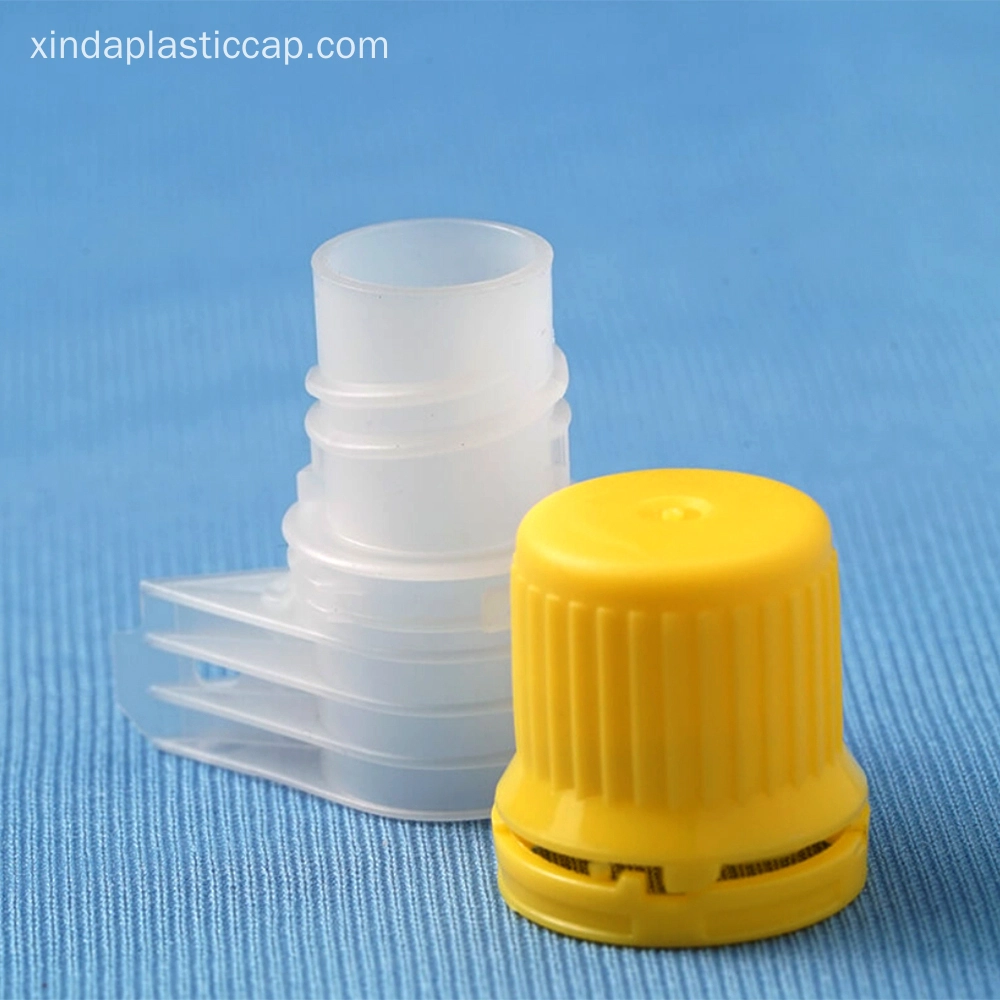
The Role of Plastic Spout Caps in Food and Beverage Packaging
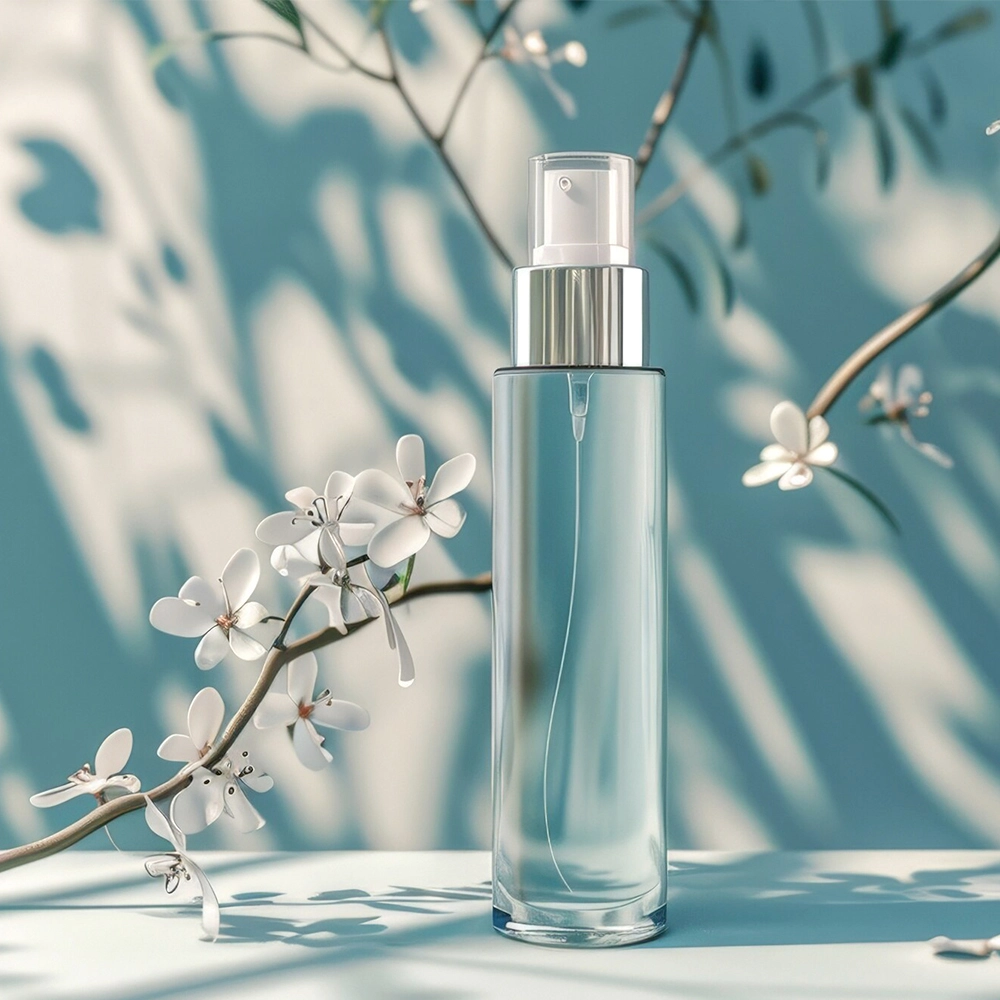
China's Top Perfume Pump Sprayer Manufacturers: Xinda Pelosi
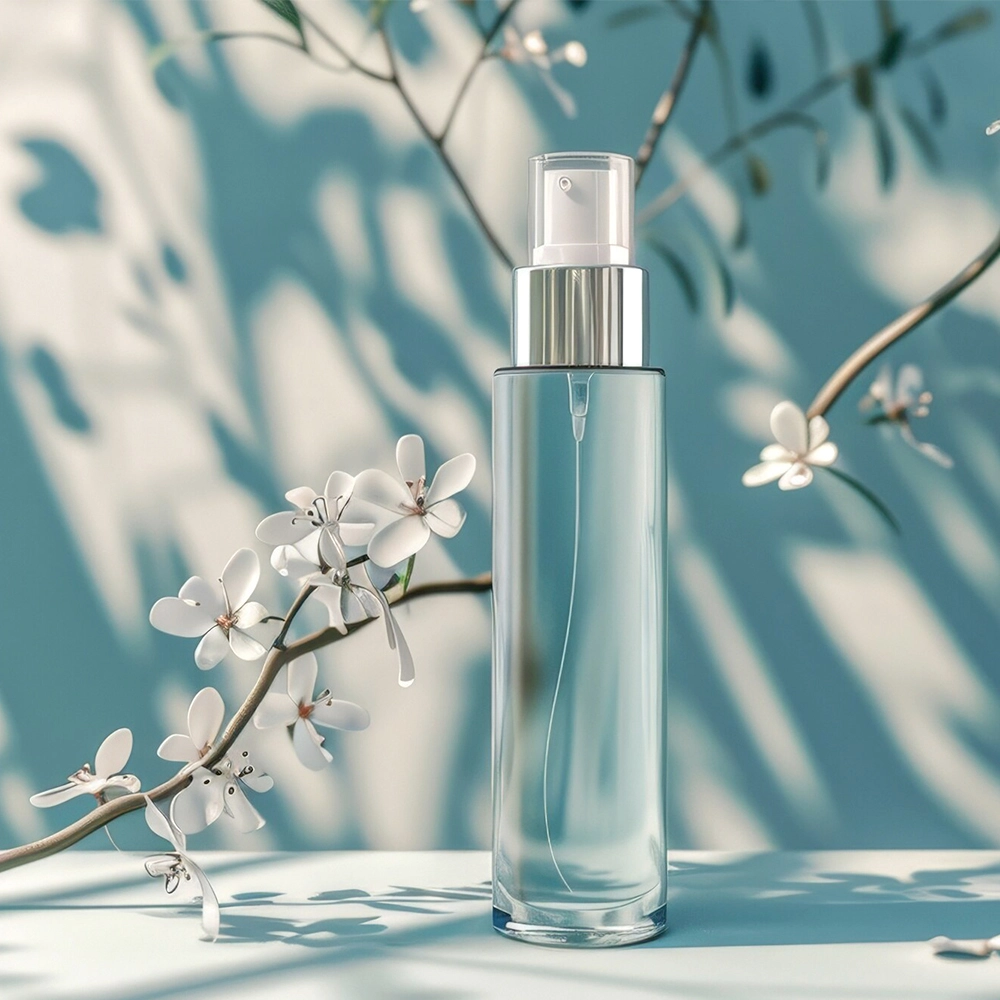
How to Choose the Size of a Travel Perfume Sprayer ?
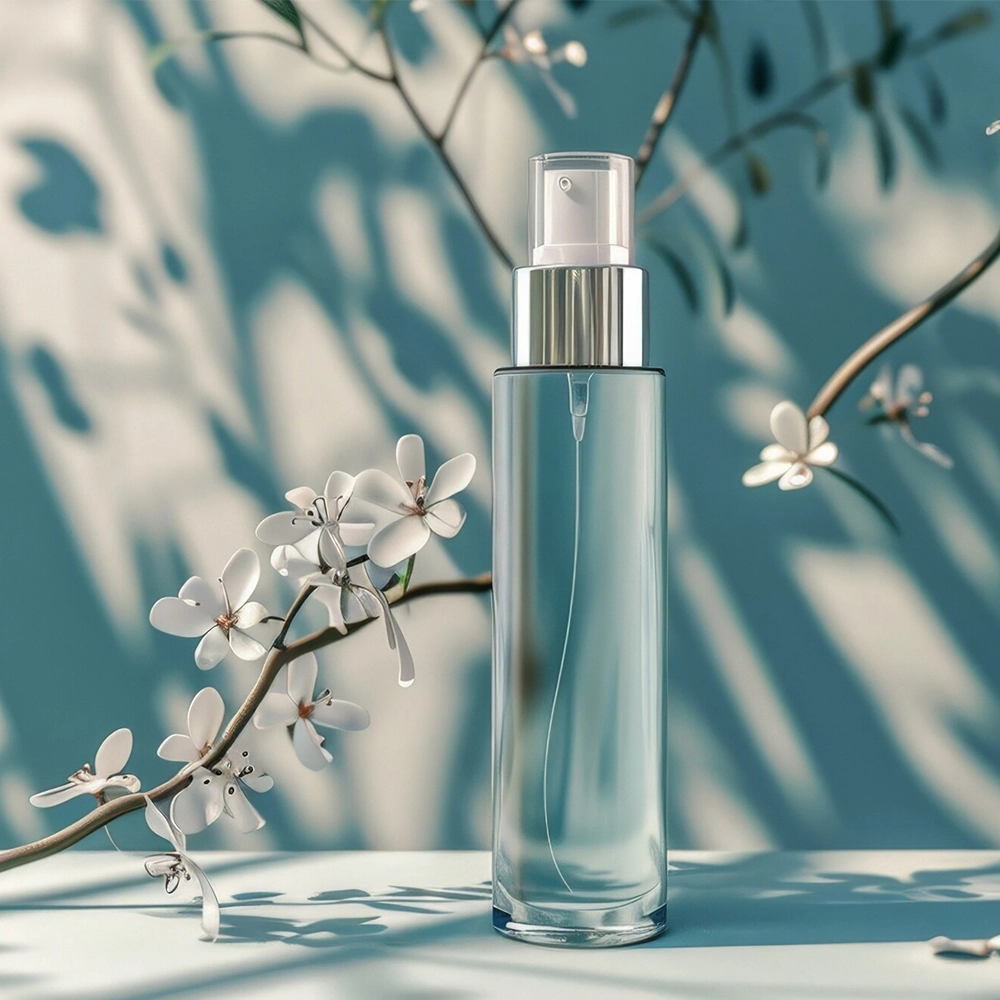
The Importance of Perfume Spray Pumps in Cosmetic Packaging: A Sustainable Approach
For after-sales
What is your aftersales policy?
When discharging the goods at the customers' end, please inspect all the cartons.
If you find any breakage or defective products, please take pictures of the original cartons. Please present the claim within 15 working days after the container is discharged. This date is subject to the arrival time of the container.
We will advise certifying the claim by the third party or accepting the claim based on the samples or pictures presented by the customers. If the damage or defect is confirmed to have been caused by us, we will replace all the goods or refund the money to the customers.
What we should do if the products have quality issues?
We would replace all the products which have quality problems.
For shipping
What are your shipping terms?
1. For small trial order,FEDEX,DHL,UPS,TNT can be provided.
2. For large orders,we can arrange shipment by sea or by air according to your requirement.
What are shipping options?
Usually, we suggest shipping by sea based on a certain quantity because it is cheaper and safer. For small quantities, we usually suggest shipping by air, which is much faster.
For Products
What value-added services can we provide?
- 1. Can make different colors and different decorations, like silk screen printing, hot stamping, UV coating, and spray coating.
2. We can do labels, new designs and molds according to your samples or pictures.
3. Samples can be provided for free.You are welcome to ask for samples to check the quality.
You may also like
We provide a variety of packaging solutions to both small and large businesses and service numerous industries, including beauty and personal care, food and beverage, household and industrial chemicals, and veterinary care.
Get in touch with Xinda pelosi
Have any questions or queries about our products? Please leave us a message here and our team will get back to you promptly.
Your inquiries, ideas, and collaboration opportunities are just a click away. Let's start the conversation.
* Rest assured that your privacy is important to us, and all information provided will be handled with the utmost confidentiality.
Whatsapp: +8613640286461