What's inside a lotion pump and how does it work? | Xinda Pelosi Guide
Discover the components of a lotion pump (actuator, spring, dip tube, valve, housing) and how they work together to dispense lotions efficiently. This article covers common issues like clogging and leaks, providing essential insights for cosmetic and pharmaceutical professionals. Understanding these mechanics improves packaging efficiency and customer satisfaction.
What's Inside a Lotion Pump and How Does It Work?
Understanding the mechanics of a lotion pump is crucial for cosmetic and pharmaceutical manufacturers. This article details the internal components and operational principles of these ubiquitous dispensing mechanisms, addressing common challenges and maintenance concerns.
The Core Components of a Lotion Pump
A typical lotion pump, regardless of size or specific design, consists of several key parts working in concert:
* The Actuator: This is the top part you press. It's usually made of plastic and transmits the force downwards.
* The Spring: Located beneath the actuator, the spring provides the necessary return force, bringing the actuator back to its original position after dispensing.
* The Dip Tube: This tube extends down into the bottle, drawing the lotion up towards the dispensing mechanism. The material and length are crucial for optimal fluid flow and preventing clogging.
* The Valve Assembly: This is the heart of the pump. It contains a spring-loaded valve that opens and closes, controlling the precise dispensing of the product. Variations in valve design affect flow rate and prevent leakage.
* The Housing: The housing encases all of the inner components, protecting them and maintaining structural integrity. It is often made of durable plastic chosen for its chemical compatibility with the product contents.
How a Lotion Pump Functions: A Step-by-Step Guide
1. Actuation: Pressing the actuator compresses the spring.
2. Valve Opening: This compression forces the valve assembly open, creating a vacuum in the chamber.
3. Fluid Ascent: The vacuum pulls the lotion up the dip tube.
4. Dispensing: The lotion is forced through the valve and dispensed through the nozzle.
5. Spring Return: When pressure is released from the actuator, the spring returns it to its original position, closing the valve and preventing leakage.
Common Issues and Troubleshooting
* Clogging: This often results from thick lotions or improper cleaning. Regular maintenance and selecting appropriate dip tubes can mitigate this.
* Leaks: Leaks usually indicate a worn-out valve or a damaged seal. Replacing the entire pump assembly might be necessary.
* Inconsistent Dispensing: This can be caused by a weakened spring or a problem with the valve assembly.
Understanding the intricate workings of a lotion pump is essential for ensuring product quality, efficient packaging, and customer satisfaction. By addressing these common challenges proactively, manufacturers can maintain production quality and avoid costly recalls.

Customize Perfume Pump Sprayer Manufacturer in Europe
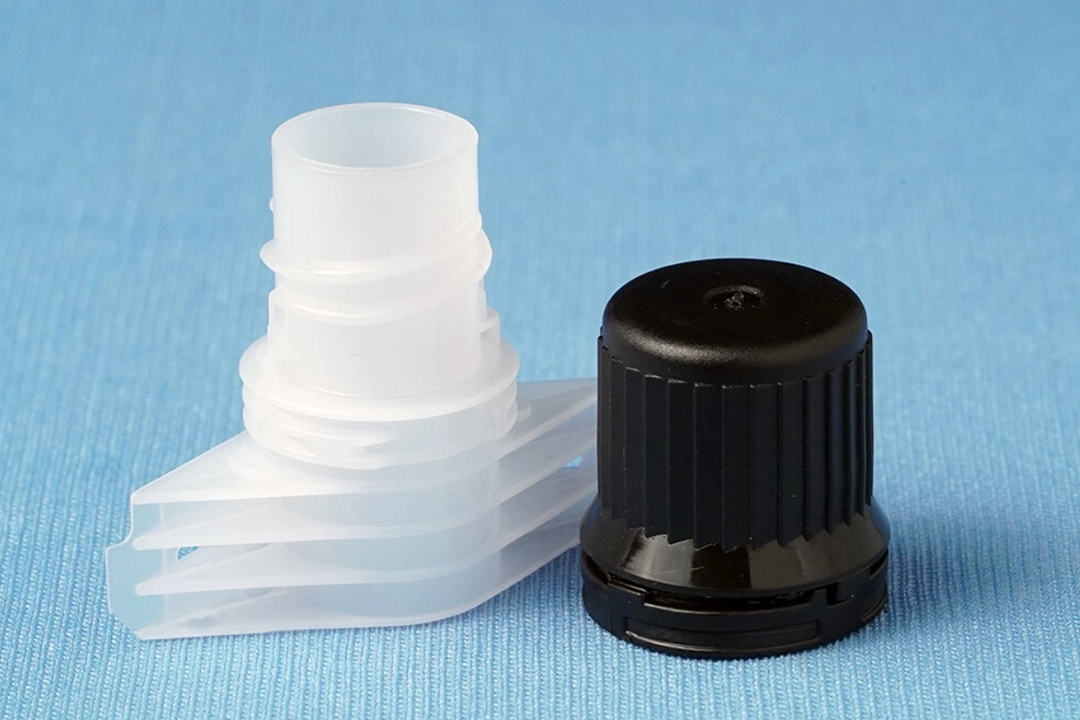
Plastic Caps and Closures Market Report 2024 (Global Edition)

How to choose a suitable supplier for flexible packaging special food grade plastic suction nozzle tube and cover?
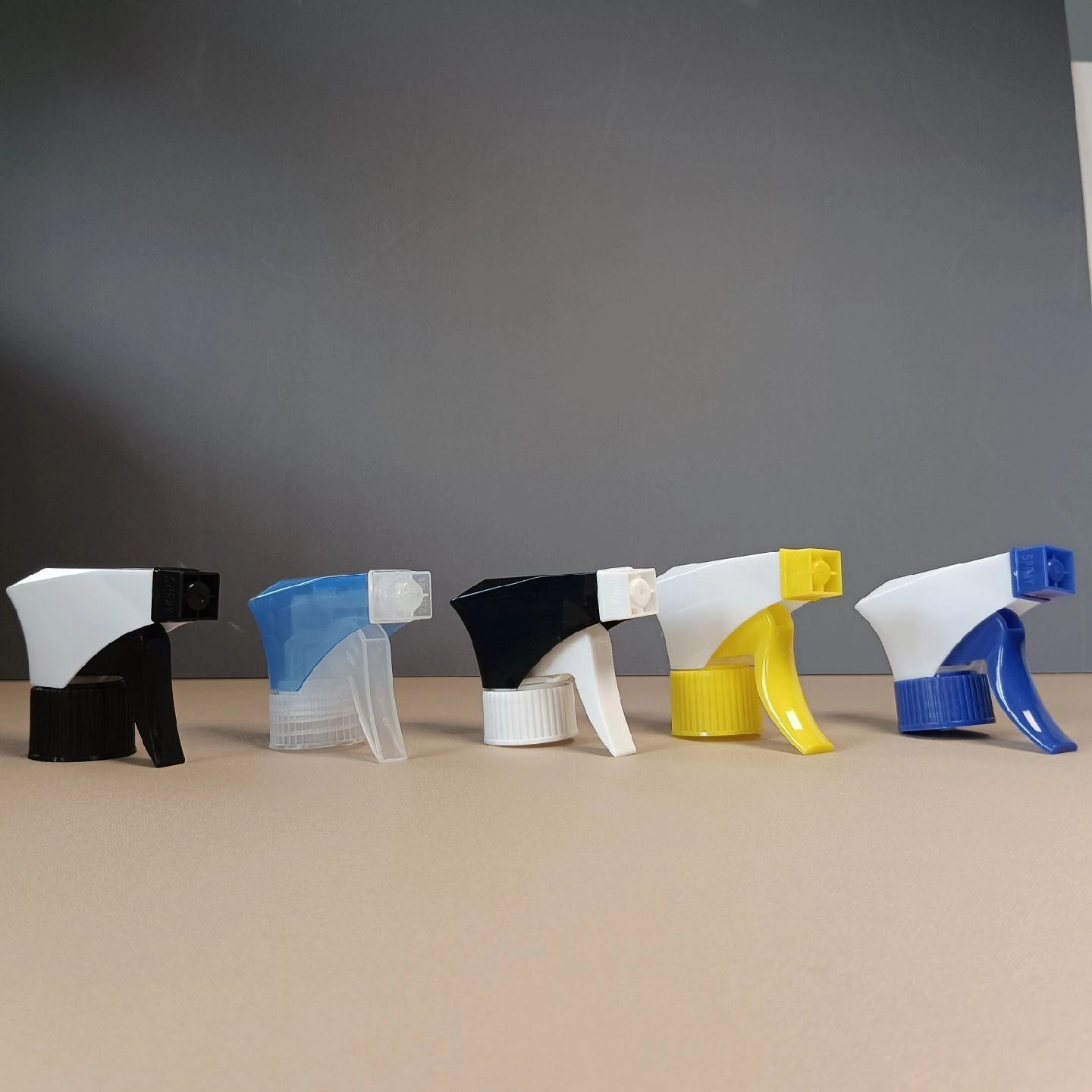
Top 10 plastic spout cap suppliers brands
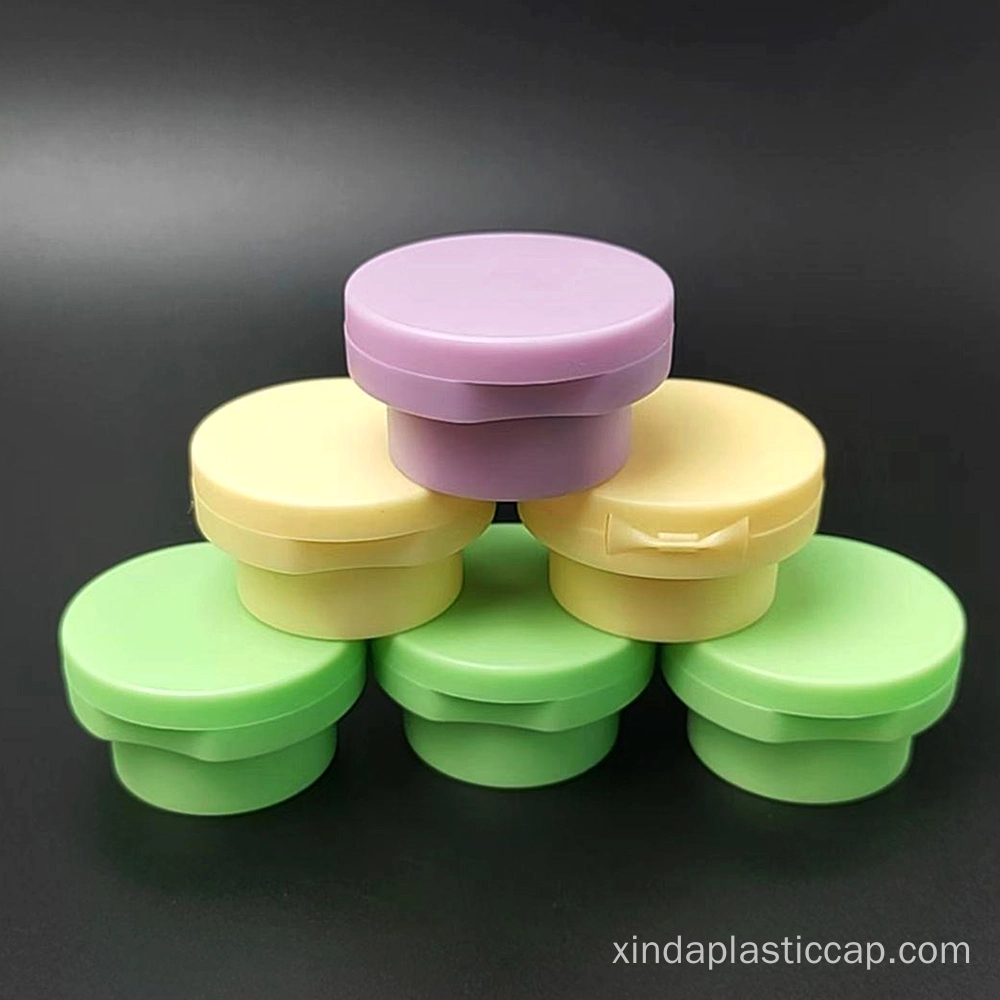
How Flip Top Cap Manufacturer Transforms Daily Use
For after-sales
What if I got some defective mold/products?
We will take full responsibility for our default. We will implement the fastest remedy to rework or reproduce on our account. As for parts, we will exchange good products or refund you immediately. If you have any questions, please feel free to contact us.
What we should do if the products have quality issues?
We would replace all the products which have quality problems.
For application
What's the applications of PP spout caps?
PP is commonly used in spout caps for a wide range of products, including food and beverage items, due to its ability to withstand various environmental conditions.
For Customization
About OEM
Welcome! You can send your own design of glass product and logo; we can open a new mold and print or emboss any logo for you.Model, size, color, logo, printing, lid, and individual packaging (paper box, paper tube and so on.) can all be customized.
What's the process of Customized product?
1. Mold design from product drawings or samples.
2. Confirm the drawings with the customer.
3. Make molds.
4. T1 test and send samples to the customer for adjustment.
5. Adjust the mold, retest and send samples to the customer for approval.
6. Receive confirmation from the customer.
7. Send out molds or arrange series production.
You may also like
We provide a variety of packaging solutions to both small and large businesses and service numerous industries, including beauty and personal care, food and beverage, household and industrial chemicals, and veterinary care.
Get in touch with Xinda pelosi
Have any questions or queries about our products? Please leave us a message here and our team will get back to you promptly.
Your inquiries, ideas, and collaboration opportunities are just a click away. Let's start the conversation.
* Rest assured that your privacy is important to us, and all information provided will be handled with the utmost confidentiality.
Whatsapp: +8613640286461