How do I clean and maintain my foam soap pump to keep it working properly? | Xinda Pelosi Guide
Learn how to clean and maintain foam soap pumps for optimal performance in custom plastic caps packaging with expert advice from Xinda Pelosi.
How do I clean and maintain my foam soap pump to keep it working properly?
Maintaining the performance of your foam soap pumps is crucial for professionals in the custom plastic caps packaging industry. This guide uses the keyword “How do I clean and maintain my foam soap pump to keep it working properly?” to address common problems such as clogging, residue build-up, and inconsistent dispensing.
Why Regular Cleaning is Essential
- Residue from soap formulas can clog foam pumps, reducing efficiency.
- Regular maintenance extends pump life and maintains consistent foam quality.
- Proper cleaning supports sustainable packaging practices by maximizing reusability.
- Industry studies (Source: Packaging Strategies, 2023) show regular cleaning can extend pump life by up to 30%.
Step-by-Step Cleaning Process
1. Disassemble the Pump
- Carefully unscrew the pump from the bottle.
- Separate all removable components (lid, pump head, tube, and spring mechanism if possible).
2. Rinse Thoroughly
- Flush components with warm water to remove surface soap and debris.
- Use a gentle brush for stubborn residue, especially in crevices.
3. Soak in Cleaning Solution
- Prepare a mild cleaning solution (1:10 white vinegar to water).
- Soak all parts for 15–30 minutes to dissolve hardened or oily residue.
4. Rinse and Dry Completely
- Rinse each part with warm water until no cleaning solution remains.
- Allow all parts to air dry thoroughly before reassembling to prevent mold growth.
5. Reassemble and Test
- Carefully reassemble all pump parts.
- Test with water to ensure smooth and consistent foam output.
Maintenance Tips for Long-Term Performance
- Monthly Deep Clean: For high-use pumps, clean monthly or after any formula change.
- Inspect Frequently: Check for cracks, discoloration, or material fatigue—replace parts as needed.
- Lubricate If Needed: Use silicone-safe lubricant to maintain spring action (refer to manufacturer guidelines).
- Store Correctly: Keep spare pumps dry and away from direct sunlight to avoid material degradation.
Common Problems and Solutions
- Clogging: Usually caused by dried soap or particulates. Follow full cleaning steps above.
- Weak Foam Output: May indicate air blockage—ensure air holes are clear, and all parts are fully dry.
- Dripping or Leaking: Check for proper assembly, O-ring positions, and ensure no cracks in plastic caps.
(Source: International Dispensing Association, 2022)
Key Takeaways for Custom Plastic Caps Packaging Professionals
- Regular cleaning of foam pumps is vital for maintaining high-performance standards in custom plastic cap packaging.
- Detailed maintenance routines help minimize downtime and preserve the quality of your packaging solutions.
- Following best practices not only promotes hygiene but also adds value to your product offerings.
For further technical resources or to request custom solutions for foam soap pumps and plastic caps, contact the experts at Xinda Pelosi.
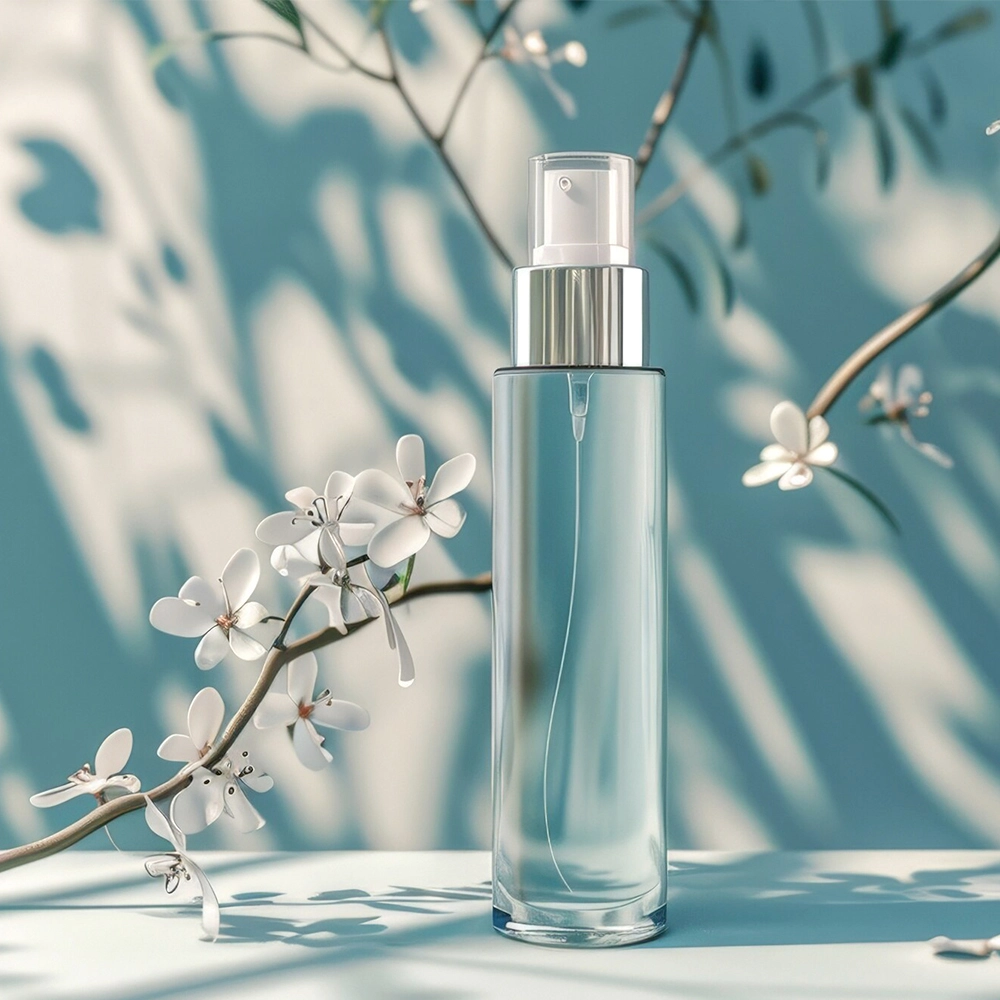
China's Top Perfume Pump Sprayer Manufacturers: Xinda Pelosi
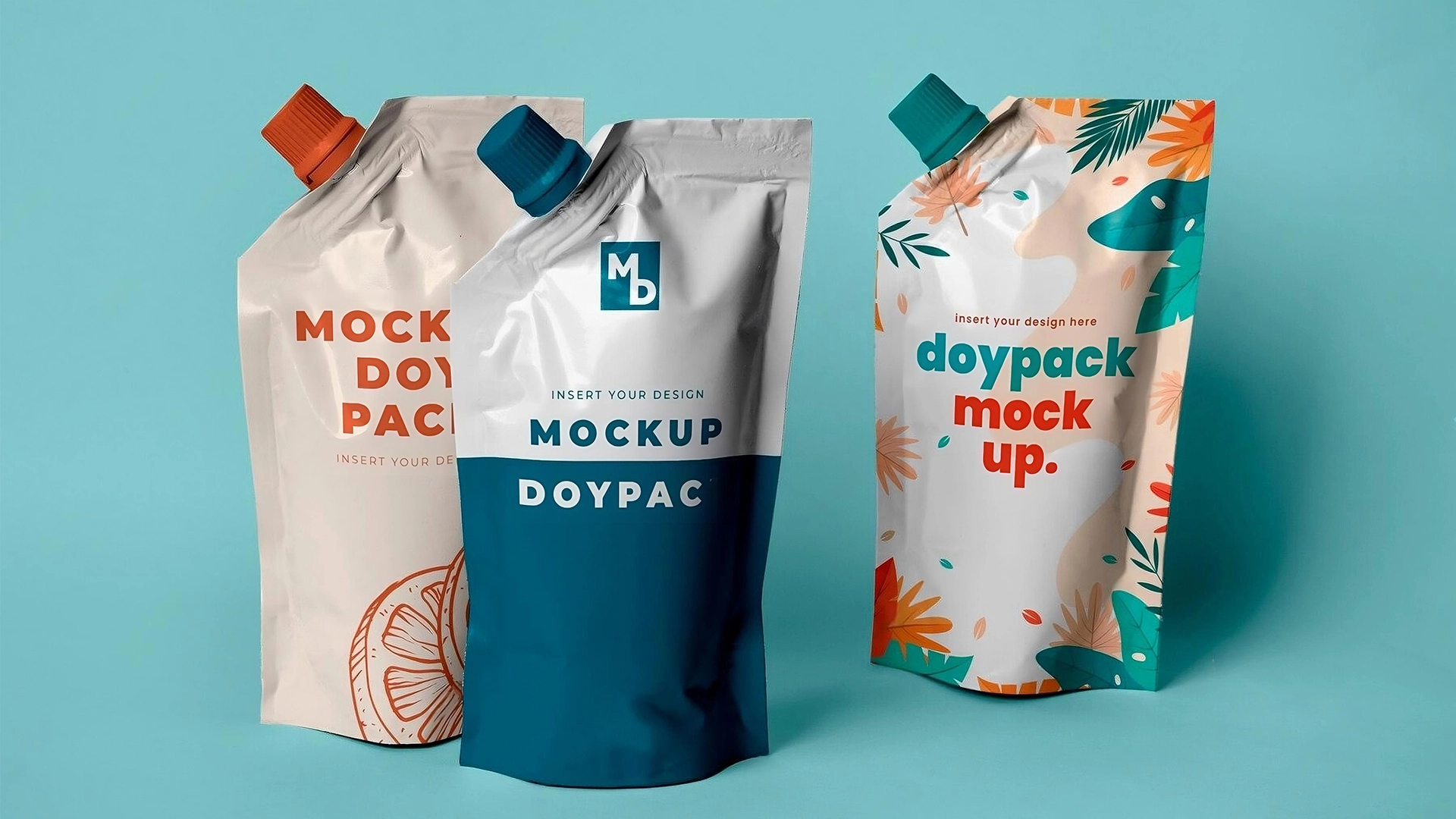
How to Boost Your Brand with Customized Plastic Spout Caps

How to Choose the Right Cosmetic Plastic Cap for Your Needs.

How to Fix Perfume Pump Sprayer
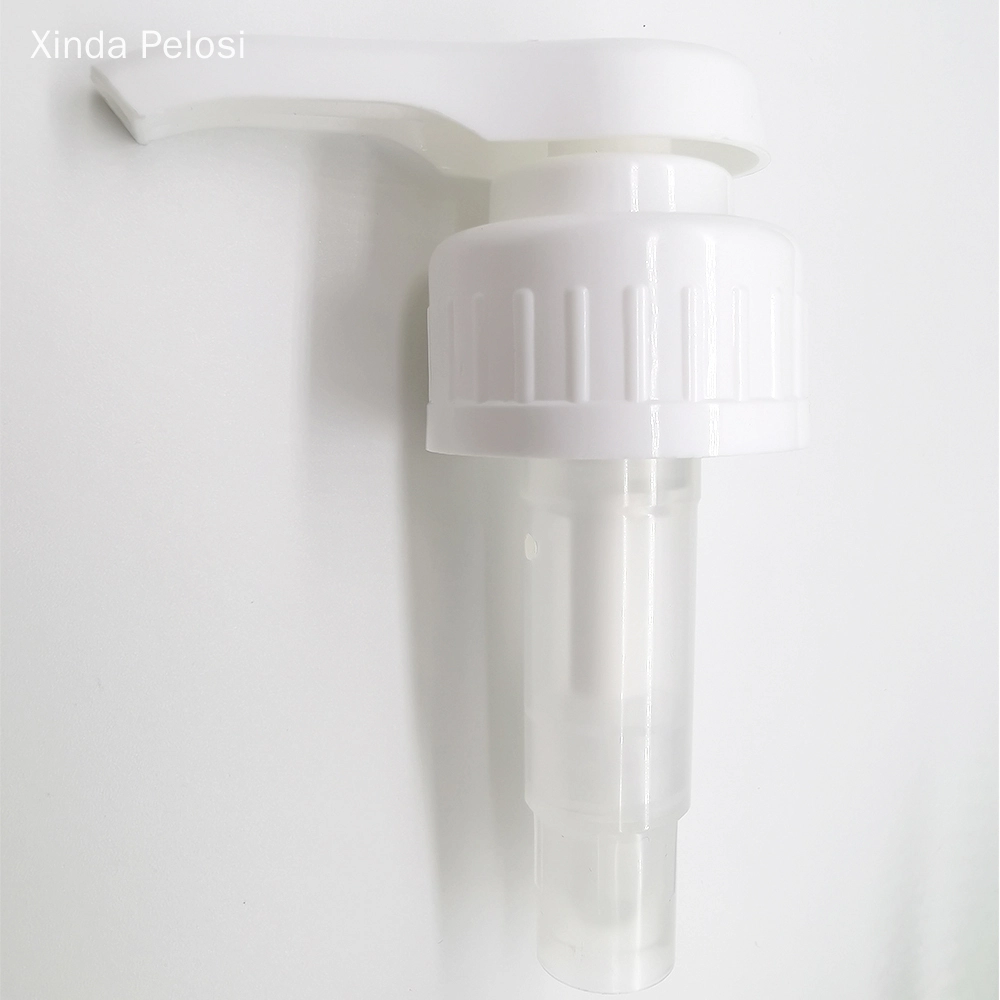
Foaming vs Regular Soap Dispensers: 6 Key Differences - Xinda Pelosi
For Customization
Could you make my own design ?
Yes, it is welcome. Please send us your design document in PDF, CDR, or AI format.
For after-sales
To whom should we send our complaint about your product or service?
Please kindly write down your complaint with all the details and send it to us.Our Complaint Handling Center will reply to you in 24 hours.
For Company
How to start a custom project with your company?
Please send us your design drawings or original samples so that we can offer a quotation first. If all details are confirmed, we will arrange the sample once we receive your deposit.
For shipping
What is your shipping way?
By sea, by air, or by express, etc. We will help you choose the best shipping method according to your specific requirements.
For application
What is the application area of the item?
Easily dispense shampoo, lotions, liquid soaps, body soap, dish soap, creams and aromatherapy/essential oil mixtures as your
idea.
You may also like
We provide a variety of packaging solutions to both small and large businesses and service numerous industries, including beauty and personal care, food and beverage, household and industrial chemicals, and veterinary care.
Get in touch with Xinda pelosi
Have any questions or queries about our products? Please leave us a message here and our team will get back to you promptly.
Your inquiries, ideas, and collaboration opportunities are just a click away. Let's start the conversation.
* Rest assured that your privacy is important to us, and all information provided will be handled with the utmost confidentiality.
Whatsapp: +8613640286461